Commercial Roofing ABCs
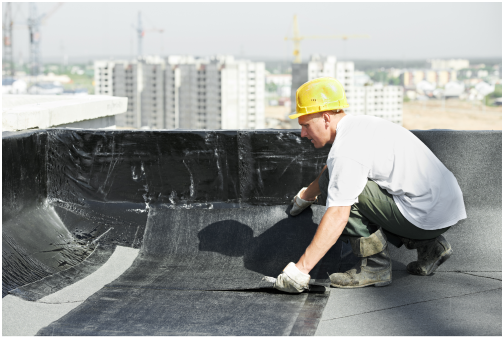
Whether you’re starting a new venture or you’ve been an entrepreneur for years, owning a business is a tall feat. For business owners who also embark on commercial real estate ownership, the demands increase even further. A commercial property presents both opportunities and challenges, but with careful consideration, the return on investment is well worth the risk.
That said, the roof of your commercial property is one component of the asset that requires regular attention to ensure your investment maximizes its potential. Many commercial roofs are installed using the wrong materials for the building’s shape or the business type. This oversight can result in grave consequences. Hiring a commercial roofing contractor in St. Louis to help with the roof installation process is a must-do. In the meantime, this short guide provides an overview of the most common types of commercial roofing systems on the market.
BUR (Built-Up Roofing)
Built-up roofing is a commercial roofing system that’s been around for years, and it’s the one you’ll find most commonly on low-slope commercial roofs. BUR is composed of reinforced fabric layers interspersed with layers of asphalt-based materials. The whole thing is topped off with a layer of gravel or some other form of aggregate. It is extremely durable and inexpensive to install. However, it lacks the energy-efficiency of other designs, such as a TPO roof.
MOD BIT (Modified Bitumen)
Similar to the BUR style, modified bitumen roofing employs a layering strategy. However, rather than interspersing asphalt-based materials with reinforced fabric layers, mod bit roofing material is rolled out in layers, which are then heat-sealed, hot- or cold-applied, or self-adhered. There’s no need for a layer of gravel; a base sheet is mechanically attached to the roof deck. Mod bit roofs also work well on low-slope roofs and are relatively easy to install. They’re a good option for businesses that may require a lot of rooftop foot traffic – it’s famously thicker than other roofing options.
TPO (Thermoplastic Polyolefin)
TPO roofs are one of the fastest-growing commercial roofing systems on the market. They’re relatively inexpensive, and since they’re white, one of the most significant advantages of a single-ply TPO roof system is its reflective properties. TPO roofs offer tremendous resistance to chemicals and UV rays and boast high marks for energy-efficiency. Installation involves rolling out single-ply membranes and then welding them to the roof seams to create a waterproof seal. Your commercial roofing contractor in St. Louis should be able to guide you in whether a TPO roof is right for your commercial property.
EPDM (Ethylene Propylene Diene Monomer)
EPDM roofs are made of a very durable synthetic rubber. Hail literally bounces right off the roof’s surface, which is why many Midwest building owners choose this roofing material for their property. It’s challenging to compare TPO vs. EPDM roofs, but the biggest differences between the two are in the installation process and the color of the completed roof. EPDM roofs are generally black, while a TPO roof is white. Since lighter colors reflect heat more efficiently, EPDM roofs often score lower on the energy-efficiency scale. However, the durability of an EPDM roof can’t be beat, making them a popular choice for St. Louis property owners. Also, EPDM installation does not require a power source, whereas TPO does.
Need Help With Your Commercial Roof? Call Shamrock Roofing and Construction!
Sorting through the endless array of commercial roofing options can be daunting, but it’s an essential first step in protecting your commercial asset. Enlisting the help of a commercial roofing contractor in St. Louis will help you narrow down your options and identify a solution that meets both your budget and your business needs. Shamrock Roofing would love to be your partner in this process. We have the experience you need to make a solid financial decision. Contact us today!